In the pharmaceutical industry, even minor oversights can lead to significant compliance failures. The Corrective and Preventive Actions (CAPA) process is essential in mitigating these risks and forms the backbone of a robust Quality Management System (QMS). However, many pharmaceutical manufacturers still struggle with effective CAPA implementation. FDA inspection data reveals that inadequate or missing CAPA procedures are frequently cited in Form 483 observations, highlighting a gap in compliance.
A well-structured CAPA program helps address quality deviations, implement corrective actions, and prevent recurrence. Ensuring it aligns with FDA regulations, such as 21 CFR Part 820.100, is crucial for its effectiveness. This blog will explore what makes a CAPA program effective, how to align it with FDA guidelines (21 CFR Part 820.100), and practical steps for execution in pharma settings.
What is CAPA?
CAPA, or Corrective and Preventive Actions, is a structured quality management process used across regulated industries, especially in pharmaceuticals, medical devices, and biotech, to investigate, resolve, and prevent the recurrence of nonconformities, deviations, or quality issues.
CAPA is governed under specific regulatory frameworks:
- 21 CFR Part 820.100 (FDA Quality System Regulation for medical devices)
- ICH Q10 (Pharmaceutical Quality System)
- ISO 13485 (Medical devices)
- ISO 9001 (General quality management systems)
Corrective Action
Corrective actions are reactive. They involve identifying the root cause of a known problem and implementing steps to eliminate it and prevent its recurrence.
Example: If a batch of drug products fails stability testing due to incorrect humidity conditions, the corrective action might include recalibrating the environmental monitoring system and retraining staff.
Preventive Action
Preventive actions are proactive. They involve identifying potential risks or issues before they occur and taking steps to eliminate the possibility of their occurrence.
Example: If trend analysis shows increasing equipment downtime, a preventive action may include upgrading to a predictive maintenance schedule before breakdowns begin affecting batch outputs.
Key Elements of an Effective CAPA System
- Identification: Recognize nonconformities or potential risks.
- Evaluation: Assess the severity, frequency, and impact.
- Investigation: Perform root cause analysis (e.g., 5 Whys, Fishbone Diagram).
- Action Plan: Define and document the corrective or preventive steps.
- Implementation: Carry out the defined actions.
- Verification of Effectiveness (VOE): Ensure the issue has been truly resolved or prevented.
- Documentation: Maintain detailed records for audit and compliance readiness.
Importance of CAPA in Various Industries
CAPA is not just a regulatory checkbox; they are essential to maintaining product integrity, consumer safety, and operational excellence across sectors. Here’s how CAPA plays a vital role in different industries:
1. Pharmaceuticals
- Why it matters: FDA expects documented CAPA processes under 21 CFR Part 211 (cGMP). Failure here can lead to 483 observations or warning letters.
- Example: Contaminated drug batches traced to poor cleaning protocols may trigger a corrective action to revise SOPs and retrain staff.
2. Medical Devices
- Why it matters: Under 21 CFR Part 820 (QSR), CAPA is central to quality assurance.
- Example: A design flaw causing device malfunction may lead to a CAPA that includes redesign, complaint trend analysis, and process validation.
3. Biotech
- Why it matters: Risk-based product development and manufacturing require proactive quality controls.
- Example: Variability in bioreactor yields could trigger a CAPA to identify and mitigate root causes, such as raw material variability or equipment malfunction.
4. Food and Beverage
- Why it matters: CAPA is a part of HACCP and FSMA compliance.
- Example: A bacterial contamination event could result in immediate corrective actions and long-term preventive measures such as supplier audits or infrastructure upgrades.
5. Cosmetics and Personal Care
- Why it matters: Though less regulated than pharma, product recalls due to skin reactions or contamination demand effective CAPA systems.
- Example: Reports of skin irritation from a product could initiate a CAPA involving reformulation and packaging safety review.
Across all these sectors, an effective CAPA process reduces the recurrence of issues, protects consumer health, avoids regulatory penalties, and supports business continuity.
CAPA vs. ISO 13485: A Regulatory Alignment
ISO 13485 is the international standard for quality management systems specific to medical devices. It places strong emphasis on the implementation of an effective CAPA system, but with distinct expectations:
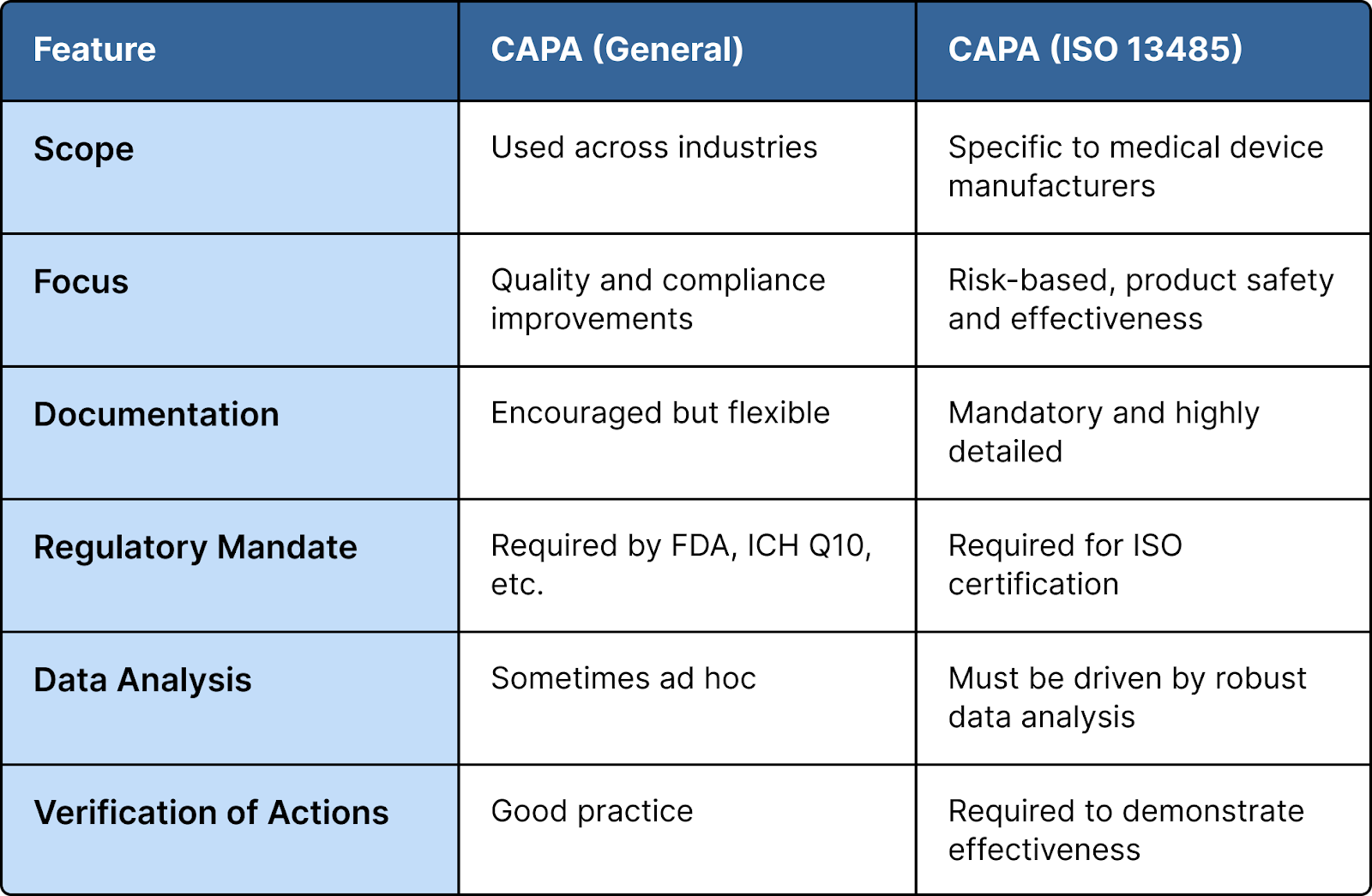
While general CAPA systems aim to fix and prevent quality issues, ISO 13485 makes CAPA a systematic, documented, and auditable process that aligns with device lifecycle risks and regulatory obligations.
7 Key Steps for Implementing a CAPA Plan
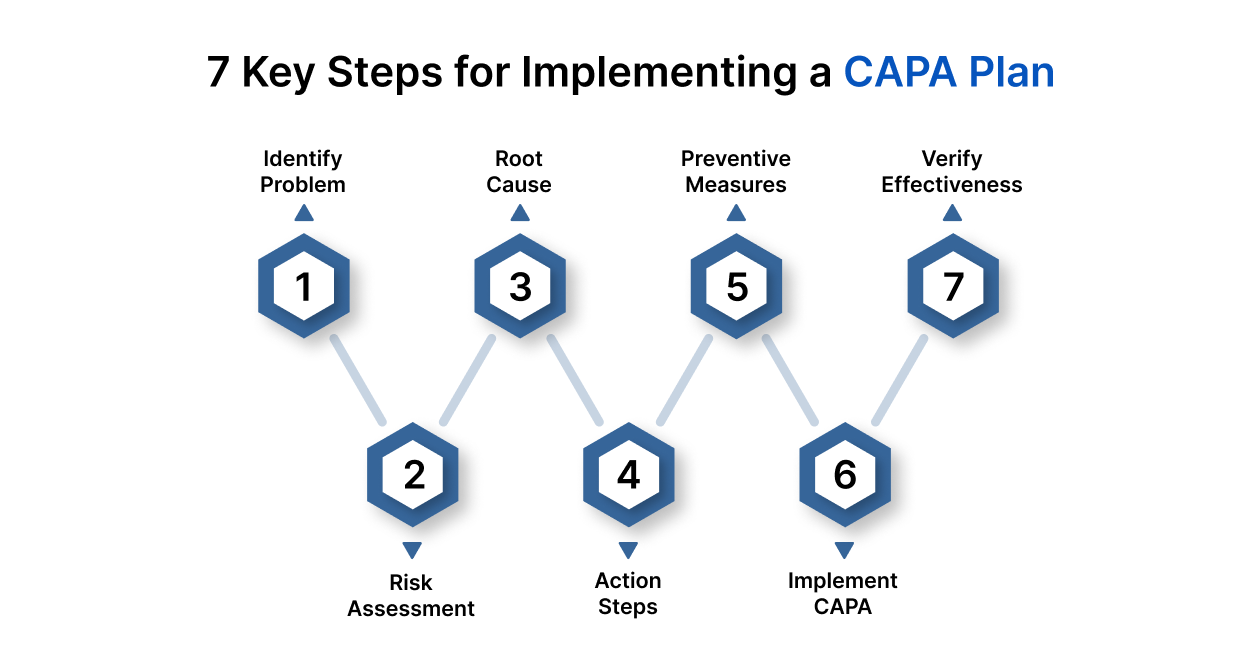
Corrective and Preventive Action (CAPA) is not just a compliance requirement, it’s a structured framework for quality control, operational excellence, and regulatory adherence.
An effective CAPA system can help avoid costly recalls, warning letters, and reputational damage. Here’s a step-by-step breakdown to help you design and implement a robust CAPA process:
Step 1. Identify the Problem
Every CAPA begins with problem identification. This could stem from a wide range of sources, nonconforming products, customer complaints, audit findings, process deviations, or recurring trends in quality data.
- Example: A spike in product returns due to packaging failure.
- Action: Log the incident in the quality management system (QMS) with clear documentation of what, when, and where it occurred.
- Why it matters: Ambiguous problem statements lead to ineffective CAPA plans.
Step 2. Assess the Risk
Risk assessment helps prioritise issues based on potential impact. Not every deviation warrants full CAPA, but serious or systemic issues must be escalated.
- Use tools like Risk Priority Number (RPN) from FMEA, or ICH Q9 risk principles.
- Evaluate severity (harm to patient), likelihood, and detectability.
- Categorise as minor, major, or critical.
Regulatory Tip: FDA expects a formal, documented rationale for determining whether a CAPA is necessary based on risk.
Step 3. Investigate the Root Cause
A CAPA plan is only as effective as its root cause analysis. This step demands thoroughness, not assumptions.
- Apply techniques like 5 Whys, Ishikawa (Fishbone) diagrams, or Pareto analysis.
- Engage cross-functional teams (QA, production, R&D) to avoid bias.
- Gather supporting data, such as batch records, logs, SOPs, training records, etc.
Avoid: Jumping to superficial causes like “operator error” without understanding why the operator failed.
Step 4. Develop Corrective Actions
Once the root cause is confirmed, develop action plans to eliminate or mitigate it immediately.
- May include equipment recalibration, retraining, process redesign, or software updates.
- Define clear timelines, responsibilities, and measurable outcomes.
- Update relevant SOPs and documents.
Example: If the issue was improper equipment cleaning, your corrective action might involve implementing cleaning verification checklists and retraining staff.
Step 5. Plan Preventive Actions
Preventive actions are proactive steps to prevent similar failures elsewhere in the system, not just fix the current one.
- Review similar processes, products, or departments for systemic vulnerabilities.
- Improve audit schedules, automation, or system alerts.
- Drive a culture of early detection (quality by design, not correction).
Tip: Regulators expect differentiation between corrective and preventive actions. Simply fixing the issue doesn’t prevent recurrence.
Step 6. Implement the CAPA
Execution requires coordination. Ensure all assigned teams understand their roles and deadlines.
- Monitor progress via a CAPA tracker or QMS dashboard.
- Escalate delays and communicate updates.
- Log all evidence: training attendance, updated documents, maintenance logs, etc.
FDA Expectation: Real-time implementation tracking and documentation during inspections.
Step 7. Verify Effectiveness
No CAPA is complete without proving it worked. Effectiveness checks ensure long-term impact.
- Monitor relevant metrics (e.g., error rates, deviations, complaints).
- Conduct follow-up audits or spot checks.
- Track for recurrence over a predefined period (e.g., 30/60/90 days post-CAPA).
Example: If retraining was the corrective action, evaluate whether error rates have reduced in the subsequent 3 months.
Step 8: Document Everything
Proper documentation is both a compliance necessity and a business safeguard.
- Include root cause, risk assessment, actions taken, effectiveness review, and final approval.
- Conduct a final review with QA or the CAPA board.
- Mark it closed only when effectiveness is confirmed, not when actions are completed.
Reminder: Incomplete or poorly documented CAPAs are among the top FDA 483 observations.
A well-developed and thoroughly documented CAPA plan is not just about compliance; it represents a commitment to continuous improvement and product quality. By following structured documentation processes and assigning clear responsibilities, businesses can reduce errors, enhance product quality, and build regulatory trust.
Sample CAPA Template
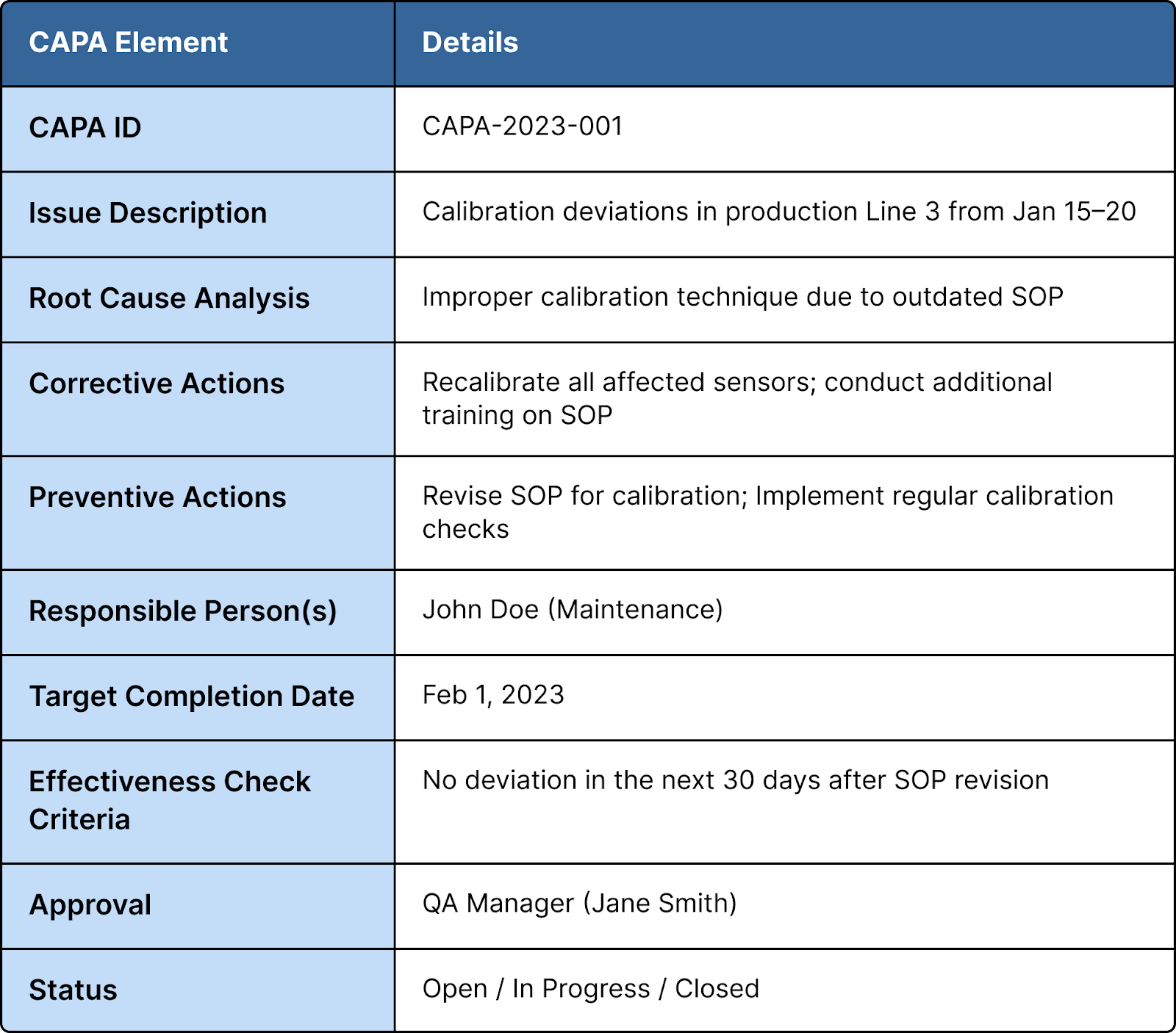
Common Challenges in CAPA Execution
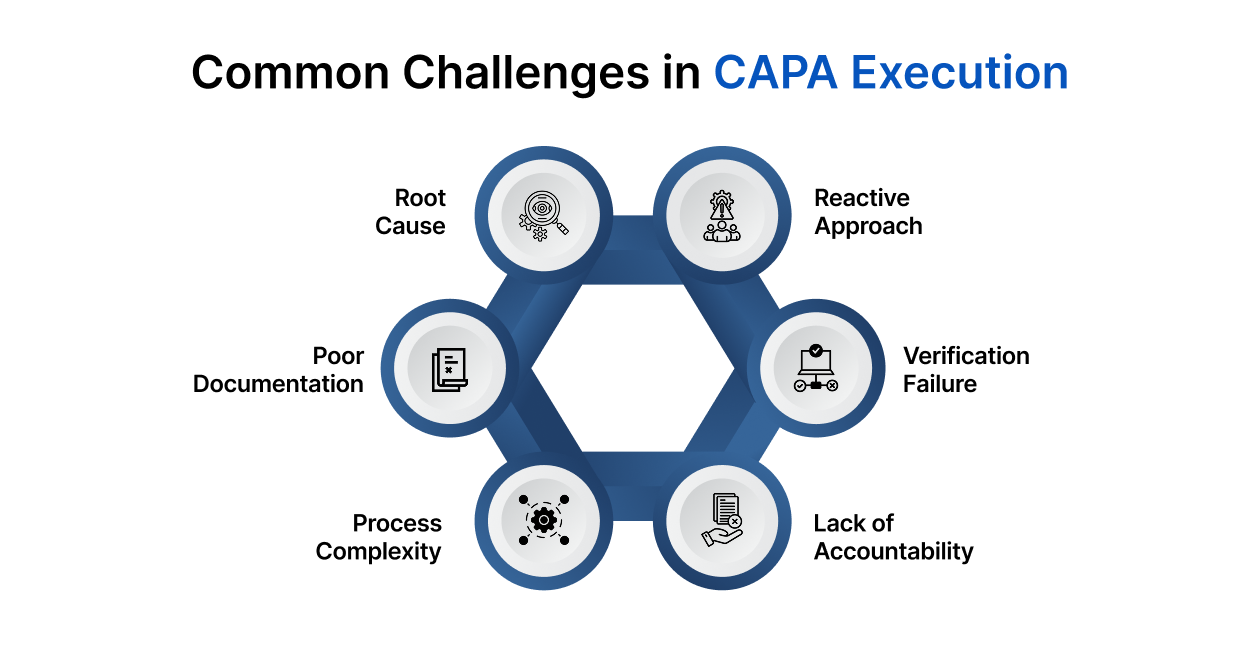
Even well-designed CAPA systems face execution hurdles that can compromise compliance and effectiveness.
- Inadequate Root Cause Analysis: Rushing this step leads to superficial fixes and recurring issues.
- Poor Documentation: Missing or vague records can lead to FDA 483 observations and incomplete audits.
- Overcomplicating the Process: Excessive forms or unclear workflows can stall CAPA progress.
- Lack of Accountability: Without assigned ownership, CAPA tasks get delayed or neglected.
- Failure to Verify Effectiveness: Skipping or rushing this phase undermines the entire process.
- Reactive, Not Preventive: Many organizations focus only on fixing issues, ignoring future risk mitigation.
Real-World Examples of CAPA
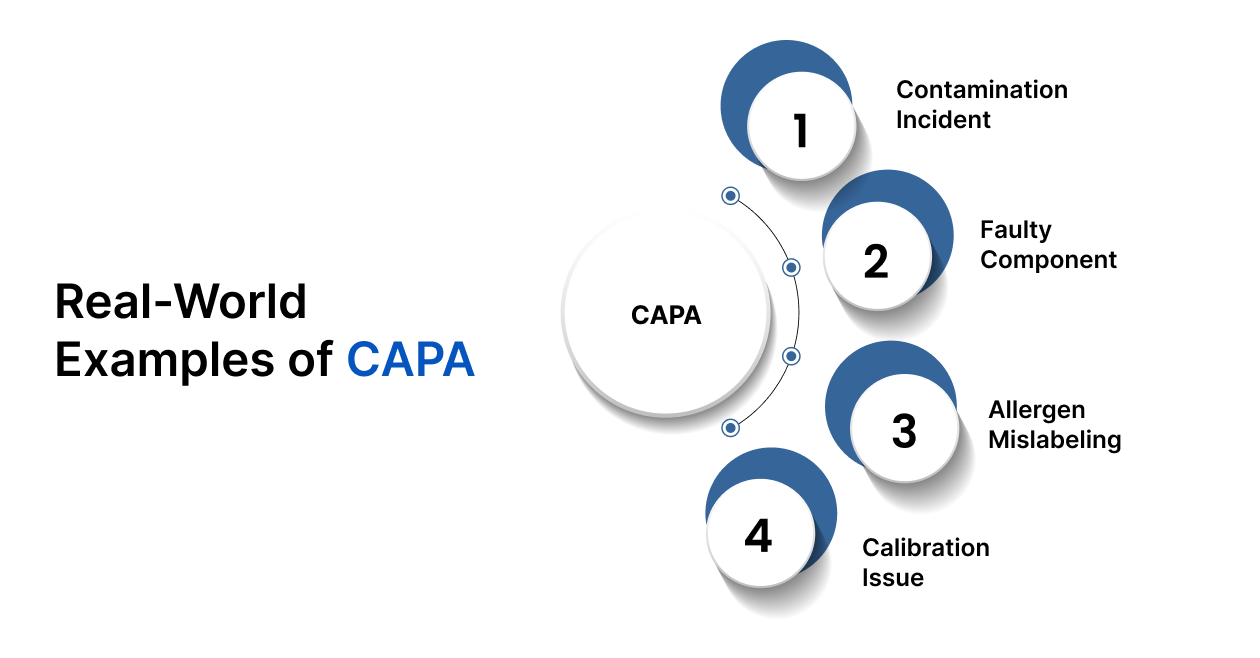
CAPA is a practical framework that prevents recurring failures. Below are examples from different industries to highlight how CAPA is applied in the real world:
1. Pharmaceutical Manufacturing: Contamination Incident
- Issue: A batch of injectable drugs was found to be contaminated during routine stability testing.
- Corrective Action: The production line was shut down; all affected batches were recalled. Root cause analysis revealed a flawed cleaning process for mixing equipment.
- Preventive Action: The company updated its SOPs, retrained staff, and introduced real-time microbial monitoring.
- Outcome: Passed subsequent FDA inspections and avoided future recalls.
2. Medical Devices: Faulty Component in Assembly
- Issue: Customer complaints revealed that a heart monitor was producing false alerts due to a sensor fault.
- Corrective Action: Investigated and identified a supplier-quality issue. All faulty products were replaced or repaired.
- Preventive Action: Supplier audit protocols were tightened, and additional incoming inspections were introduced.
- Outcome: FDA closed the complaint with no warning letter issued.
3. Food Industry: Allergen Mislabeling
- Issue: A packaged snack was found to contain undeclared peanuts.
- Corrective Action: The product was immediately recalled, and a full investigation was conducted.
- Preventive Action: Barcode scanning was implemented in packaging lines to prevent mislabeling, and label checks became mandatory before release.
- Outcome: Strengthened brand credibility and avoided regulatory penalties.
4. Biotech Lab: Equipment Calibration Failure
- Issue: A spectrophotometer used in sample analysis was found out of calibration, affecting data accuracy.
- Corrective Action: Data was re-evaluated; faulty results were invalidated and retested.
- Preventive Action: Calibration intervals were shortened, and an automated reminder system was implemented.
- Outcome: Improved audit readiness and laboratory data integrity.
These real-world CAPA examples highlight its role in risk mitigation, regulatory compliance, and operational excellence.
How Atlas Compliance Can Help with CAPA
Understanding CAPA requires more than just a checklist; it demands insight, structure, and industry-aligned execution. This is where Atlas Compliance steps in as your trusted partner.
1. CAPA System Design & SOP Development
We help you build a CAPA framework tailored to your industry, whether it’s pharmaceuticals, biotech, medical devices, or food manufacturing. Our team assists in drafting standard operating procedures (SOPs) that align with FDA, ISO 13485, ICH Q10, and other global regulations.
2. Root Cause Analysis (RCA) Support
Atlas provides tools and training to help your teams conduct effective root cause analysis using proven methodologies like 5 Whys, Fishbone Diagrams, or FMEA. We ensure investigations are thorough, evidence-based, and audit-ready.
3. CAPA Documentation & Tracking Tools
We implement document control strategies that allow you to track every CAPA from identification to closure. Our digital tracking systems reduce manual errors, improve traceability, and ensure that timelines and corrective measures are clearly recorded.
4. Training and Culture Building
CAPA only works when your people do. Atlas offers targeted training for quality and compliance teams on how to identify, report, and address non-conformities proactively, encouraging a culture of continuous improvement.
5. Audit Preparation & Mock Inspections
With Atlas by your side, you’re always inspection-ready. We conduct mock audits to test the integrity of your CAPA system, identify gaps, and prepare you for regulatory scrutiny, from FDA and EMA to ISO auditors.
6. Remediation and Follow-Up Oversight
Post-audit or after an inspectional observation (e.g., 483 or Warning Letter), Atlas helps you design and implement corrective actions that stand up to regulatory review. We support you in preparing well-structured responses that reflect accountability and compliance maturity.
A weak CAPA system is one of the top reasons for FDA warning letters and ISO certification delays. Atlas Compliance ensures your CAPA program is not only compliant but also strategic, sustainable, and scalable.
Let’s build a smarter CAPA system, together.
Conclusion
Implementing an effective CAPA system isn’t just about checking boxes, it’s about building a culture of accountability, continuous improvement, and regulatory excellence.
Atlas Compliance helps you do more than just respond to problems, it empowers your teams to prevent them. With their customized compliance solutions, expert guidance, and audit-ready documentation support, you can turn every quality incident into an opportunity for growth.
Ready to make your CAPA process bulletproof? Connect with Atlas Compliance today and take control of your quality and regulatory systems before the next audit does.